
Arc Flash Mitigation
We Offer Arc Flash Risk Assessment in all 50 States!
Good safety practices take place long before any work is slated to be performed. Electrical Safety and Arc Flash Safety is not any different. The majority of businesses today that are striving to provide a safe workplace and comply with today’s electrical standards are already in operation. In these cases, performing an Arc Flash Analysis and Equipment Labeling is a process that takes place long after the design of a power system. By designing an electrical system from the beginning with Arc Flash and Electrical Safety in mind, many risks associated with Arc Flash can be mitigated or eliminated altogether.
Arc Flash In The Design Process
The three main items that contribute to the magnitude and effect of an Arc Flash Incident are based upon the magnitude of the fault current, the time duration of the arcing event and how close a worker’s body is in proximity to the fault. How close a worker’s body is to the fault cannot always be changed based upon the type of work being performed. However, the other two items (fault current magnitude and arcing duration) can be affected by the design of the power system. The design of the power system has to be carefully thought out with special regard to lowering fault current throughout a facility and increasing speed of over-current devices.
Introducing multiple unit substations to distribute power rather than one very large transformer feeding an entire facility, actually lowers facility-wide fault current while offering greater reliability.
Implementing High Resistance Grounding to step-down transformers is a great way to prevent three-phase faults from forming due to arcing. Statistics show that the majority of three-phase arcs are started by single-phase arcing. Introducing High Resistance Grounding or a Neutral Ground Resistor virtually eliminates Arc Flash Incidents by eliminating the main cause of three-phase arcs.
Proper care and attention should be taken when selecting Over-Current Protective Devices (OCPD) for a power system. Selection of devices and features can have a drastic affect on the fault clearing times for a system. Considering the fundamental argument of fuses vs. breakers should always be considered. Most power systems utilize a combination of fuses and breakers. Tuning the system OCPD coordination to ensure proper selectivity for over-current operation, while offering robust system reliability can, in many cases, be considered an art. Proper coordination of devices should provide a reliable system under normal load and a safe system under electrical faults.
Choose appropriate OCPD sizes. Installing the lowest-ampere fuse or breaker required for downstream loads helps to ensure that the OCPD will operate in its fastest capacity. For fuses it helps to ensure operation in the Current-Limiting range if available and breaker help the ensure operation in the instantaneous region.
Choose Breakers with Adjustable Set-points. By properly adjusting breaker settings to the actual load, as well as understanding where the system fault current reaches the instantaneous band of the breaker, can lead to faster clearing times.
Consider Newer Technologies. Consider what new technologies are available during the design process. Some examples include, UV light sensing relays and trip devices, Breakers with the availability of a “Maintenance Setting” to operate at optimal time for safety but not for normal operations, remote switching and operation, etc.
For existing facilities and power systems, all of the afore mentioned can be implemented, but usually come with a higher price tag and major system alterations.
OCPD Maintenance Is The Key
A proper designed system is only as good as the installation and maintenance that it has undergone. Installation, in accordance with the NEC, helps to ensure a safe productive installation. However, once electrical equipment is installed, many times it is not maintained properly. Improperly maintained OCPD’s can lose their ability to operate at its rated ability and in many cases become completely inoperable after several years without proper maintenance. OCPD’s that operate at less than optimum values, or fail to operate at all, can lead to increased arcing time and higher Incident Energy levels.
Properly maintaining electrical equipment can even lead to Arc Flash Incidents being avoided altogether. The maintenance process often leads to eliminating causes of Arcing Faults even before the arc started. Hot spots, loose connections, depleting integrity of insulating material, all of those can be avoided or corrected before a fault occurs. Proper maintenance of OCPD’s coupled with frequent Infrared Scans can eliminate most problems.
For information on maintaining a power system, there are several standards available. The NFPA 70B “Recommended Practice for Electrical Equipment Maintenance” covers all aspects of maintenance and is recognized by industry. NETA also has a document available as well as the IEEE Blue Book that focus on Low Voltage Breakers could also be referenced. OSHA has not mandated any of these practices or standards at this time, so the process and cost of maintenance is completely voluntary. However, properly maintaining electrical equipment leads to increased worker safety, equipment reliability, and helps to eliminate the high costs of equipment failure, worker injury, and production loss.
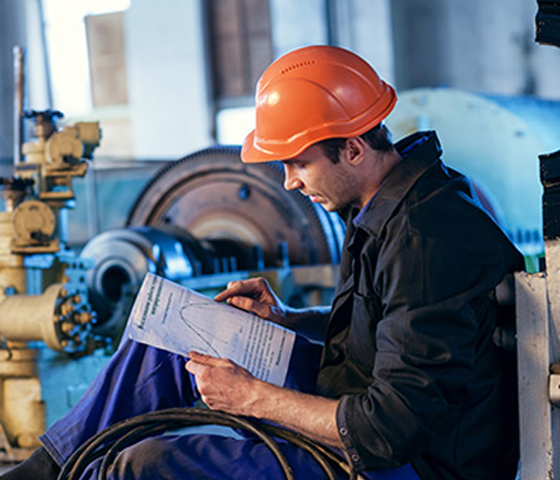
Specialization
EDS specializes in many different aspects of electrical training and engineering.
Affordable Price
All training courses are available in affordable prices.
Free Estimation
To get a free no obligation quote, please email us your details or call us and we will get back to you the same day.